Unlocking the Power of High Pressure Die Casting Moulds in Modern Metal Fabrication
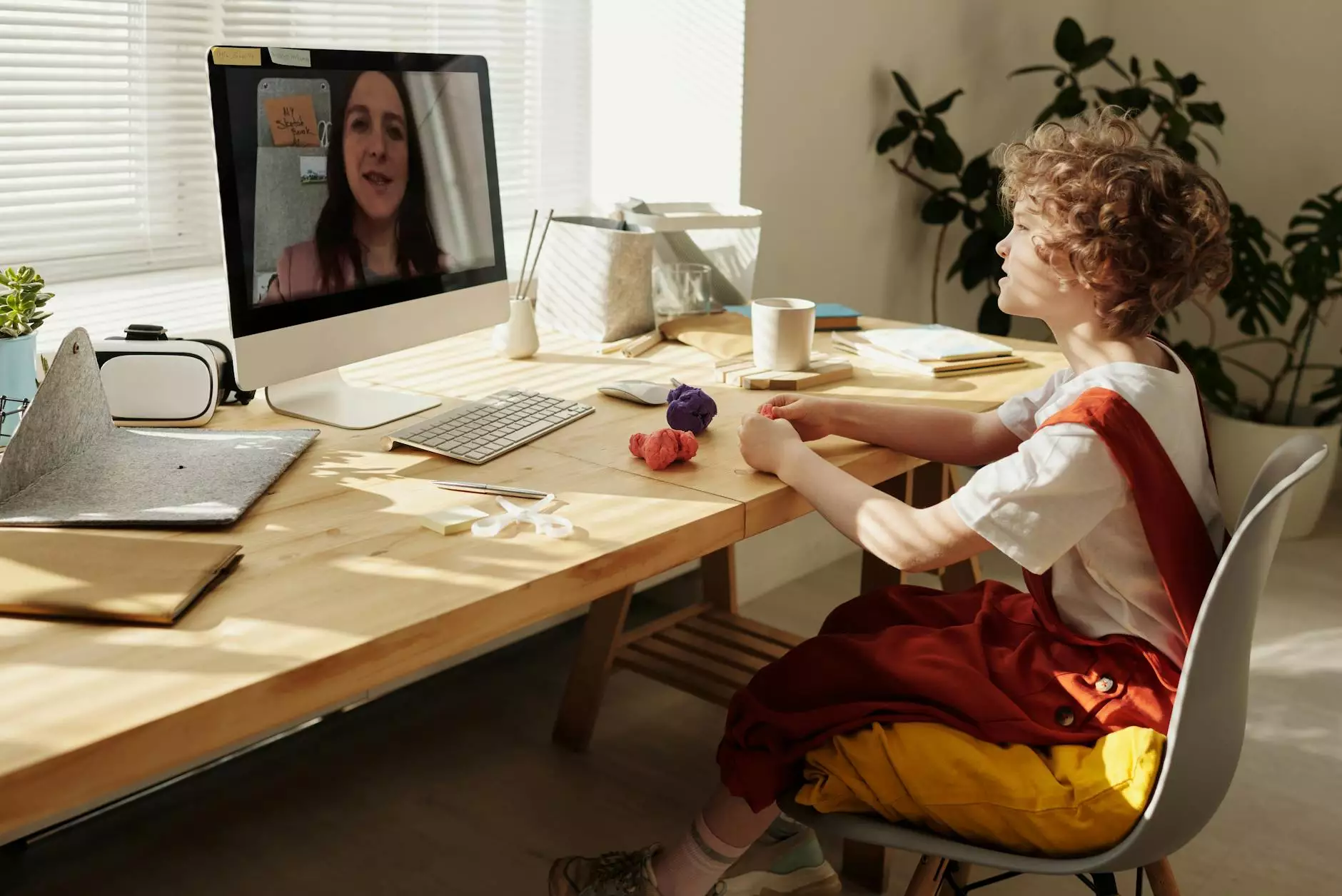
In the highly competitive landscape of metal manufacturing, the choice of moulding technology can significantly influence product quality, production efficiency, and overall operational costs. Among the myriad of casting methods available today, high pressure die casting mould stands out as a cornerstone for producing precision, high-strength metal components at scale. This comprehensive guide explores the intricate details of high pressure die casting moulds, their advantages, design considerations, materials, maintenance, and the pivotal role they play in empowering metal fabricators to excel in their industry.
Understanding High Pressure Die Casting Mould: The Foundation of Modern Metal Manufacturing
At its core, a high pressure die casting mould is a specialized tooling apparatus used in the process of high pressure die casting (HPDC). This method involves forcing molten metal—commonly aluminum, zinc, magnesium, or their alloys—into a precisely machined steel mould under high pressure, typically ranging from 1,000 to 20,000 atmospheres. The intense pressure guarantees that the metal fills every cavity of the mould uniformly, resulting in components with exceptional detail, surface finish, and dimensional accuracy.
What Makes High Pressure Die Casting Moulds Unique?
- Precision Engineering: Crafted with painstaking attention to detail, these moulds enable the production of complex geometries with tight tolerances.
- Durability & Longevity: Built using high-grade tool steels and innovative alloys, they withstand high operational stresses, ensuring long service life.
- Efficiency: Designed for rapid cycle times, they enable high-volume production with consistent quality.
- Versatility: Suitable for producing a wide range of intricate metal parts, from automotive components to consumer electronics.
Design Considerations for High Pressure Die Casting Moulds
Developing an effective high pressure die casting mould requires a meticulous approach to design, which directly impacts productivity, quality, and cost. Here are key factors to consider in design:
Material Selection
The choice of steel or alloy for the mould determines its durability and resistance to wear. Common materials include H13 hot work steel, S136, or traditional P20 steels, often treated with surface coatings to enhance lifespan and release properties.
Mould Geometry & Part Design
Optimizing the cavity design involves balancing the complexity of the component with manufacturability. Incorporating features like draft angles, fillets, and uniform wall thicknesses reduces defects and eases ejection.
Cooling System Integration
Implementing efficient cooling channels ensures uniform solidification and minimizes cycle times. Proper placement is critical to prevent warping, porosity, and surface defects.
Ejection Mechanisms
Designing reliable ejection systems, such as ejector pins or lifters, prevents damage to the delicate features of castings and extends mould lifespan.
The Manufacturing Process of High Pressure Die Casting Moulds
1. Mould Design & Engineering
Utilizing advanced CAD/CAM software, engineers create detailed 3D models of the mould, simulating the casting process to identify potential issues before production begins.
2. Material Preparation & Machining
High-quality steels are precision-machined to produce the cavity, core, and cooling channels. EDM (Electrical Discharge Machining) and CNC milling are common methods to achieve intricate features.
3. Surface Treatment & Coatings
Hardening, polishing, and applying specialized coatings like TiN or chromium nitride enhance wear resistance, facilitate part ejector, and improve surface finish.
4. Assembly & Testing
After machining, the components are assembled, and the mould undergoes rigorous testing—often with prototype castings—to ensure conformity to specifications and performance standards.
Advantages of Employing High Pressure Die Casting Moulds in Metal Fabrication
Implementing high pressure die casting mould technology offers a multitude of benefits:
1. Superior Dimensional Accuracy & Reproducibility
Achieve intricate detailing and consistent quality across large production runs, essential for industries demanding high precision, such as aerospace, automotive, and electronics.
2. Excellent Surface Finish
The process and mould design yield smooth, mirror-like surfaces, reducing the need for post-processing and finishing operations.
3. High Production Rates & Reduced Cycle Times
Rapid cooling and precise moulding cycles significantly boost output volume while maintaining tight quality controls.
4. Material Efficiency
High pressure moulding minimizes waste and scrap, optimizing material usage and lowering costs.
5. Complex Geometries & Thin-Walled Structures
From intricate internal channels to lightweight components, mould design enables the manufacture of complex parts previously difficult or impossible to produce economically.
Maintenance & Longevity of High Pressure Die Casting Moulds
Durability and continuous performance depend on proper maintenance practices:
- Regular Cleaning: Prevent buildup of casting residues and oxide layers that can impair mould function.
- Surface Inspections: Routine checks for cracks, wear, and corrosion encourage timely repairs.
- Lubrication & Coatings: Use appropriate lubricants and surface coatings to reduce friction and thermal stresses.
- Proper Storage: Store in controlled environments to prevent rust and damage.
Investing in high-quality high pressure die casting moulds with scheduled maintenance leads to fewer downtimes and extended service life, ultimately reducing long-term operational costs.
Innovations & Future Trends in High Pressure Die Casting Mould Technology
The industry continually evolves, integrating cutting-edge innovations to enhance capabilities:
- Computer-Aided Engineering & Simulation: Advanced software predicts casting behavior, reducing trial-and-error in mould design.
- Advanced Alloys & Coatings: New materials increase wear resistance and thermal stability.
- Automation & Robotics: Automated systems streamline mould handling, casting, and maintenance processes.
- Environmental Considerations: Eco-friendly alloys and energy-efficient cooling reduce the environmental footprint.
Why DeepMould.net Is Your Ideal Partner for High Pressure Die Casting Moulds
DeepMould.net specializes in designing, manufacturing, and maintaining high-pressure die casting moulds tailored for diverse industrial applications. Their commitment to quality, innovation, and customer satisfaction makes them a leader in the metal fabricators industry.
With a team of expert engineers and state-of-the-art facilities, DeepMould.net ensures that every mould meets the highest standards of precision and durability, enabling clients to maximize their production efficiency and product quality.
Conclusion: Embrace the Future with High Pressure Die Casting Moulds
In the competitive world of metal fabrication, leveraging the latest high pressure die casting mould technology unlocks new levels of efficiency, precision, and innovation. By investing in high-quality moulds, understanding the critical design factors, and maintaining the equipment diligently, manufacturers can achieve superior product outcomes, reduce costs, and stay ahead of market demands.
DeepMould.net stands ready to be your trusted partner in navigating this complex but rewarding landscape, providing expertly crafted high pressure die casting moulds that transform your manufacturing processes and open doors to new possibilities.