Comprehensive Guide to Tubing Fitting Sizes: Ensuring Precision in Fluid Connections
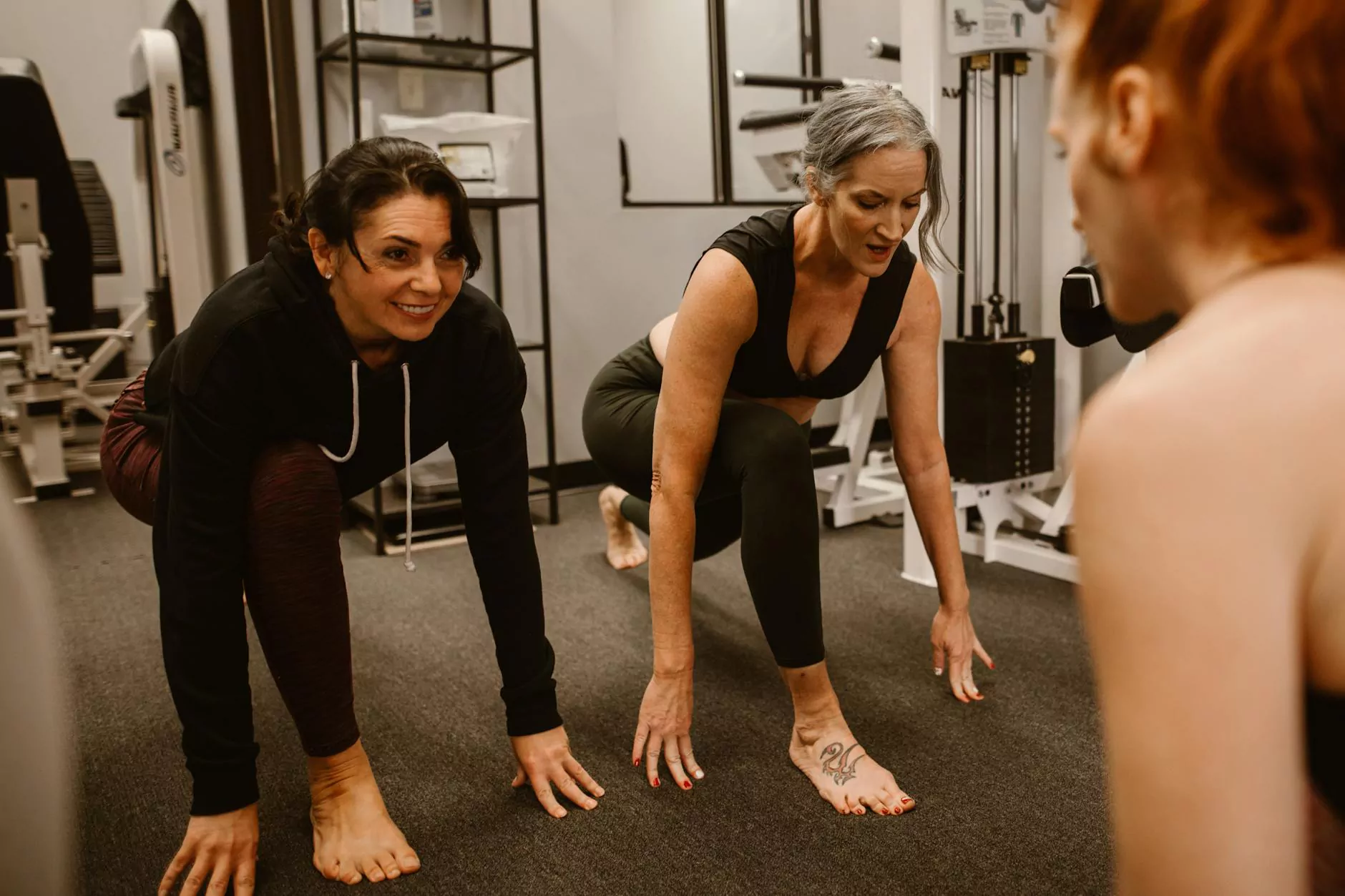
In the realm of hydraulic and pneumatic systems, tubing fittings play a crucial role in creating secure, leak-free connections that ensure the smooth operation of fluid systems. Whether you are an engineer, technician, or purchasing manager, understanding the intricacies of tubing fitting sizes is essential for selecting the right components and optimizing system performance. This exhaustive guide will cover everything you need to know about tubing fitting sizes, including types, standards, measurement techniques, and practical application tips, making it an indispensable resource for professionals aiming for excellence in fluid connection solutions.
Understanding the Importance of Accurate Tube Fitting Sizes
Tube fitting sizes are fundamental to creating reliable and efficient fluid systems. Incorrect sizing can lead to leaks, pressure drops, system failures, and costly downtime. Precise sizing ensures that fittings match the tubing dimensions perfectly, guaranteeing a tight seal and optimal flow characteristics. As industries continue to demand higher efficiency and safety standards, the importance of understanding tubing fitting sizes cannot be overstated.
Types of Tubing Fittings and Their Size Standards
1. Tube Fittings: An Overview
Tube fittings come in various configurations designed to connect, control, and direct fluids within a system. They are classified by the type of connection, material, and the fitting’s purpose. The most common categories include
- Ferrule fittings
- Forged pipe fittings
- Threaded pipe fittings
- Flanges
- Valves
2. Key Standards Governing Tube Fitting Sizes
The industry relies on standardized measurement systems to ensure compatibility and interchangeability. Major standards include:
- ANSI/ASME B1.20.1: NPT (National Pipe Thread); common for threaded fittings.
- ISO 8434: International standard for compression fittings, including ferrule types.
- DIN 2353: European standard for tube fittings.
- JIC/SAE 37° Flare: Used for high-pressure hydraulic applications.
- BS EN 10255: British standard for pipe fittings.
Understanding these standards helps in selecting the correct tubing fitting sizes for your application, ensuring compatibility and safety.
Measuring and Determining Tube Fitting Sizes
1. Outer Diameter (OD) and Inner Diameter (ID)
The primary parameters for tubing fitting sizes are the outer diameter (OD) and inner diameter (ID) of the tubing. Accurate measurement of OD is critical, as most fittings are designed to snugly fit over or inside the tubing based on these dimensions.
2. Thickness and Wall Diameter
The wall thickness of the tubing affects the selection of fittings, especially for high-pressure systems. Thicker walls require fittings with appropriate grip ranges.
3. Standard Sizing Metrics
Fittings are often specified using nominal pipe size (NPS), outside diameter (OD), or metric dimensions in millimeters (mm). For example:
- 1/4 inch tubing typically has an OD around 0.25 inches.
- 6 mm tubing corresponds approximately to 6 mm OD.
Measuring your tubing with precise calipers ensures correct fitting selection, avoiding leaks and system failures.
The Role of Tube Fitting Sizes in Different Applications
1. Hydraulic and Pneumatic Systems
In high-pressure applications, tubing fitting sizes must withstand enormous forces without deforming or leaking. Fittings such as double ferrule tube fittings and single ferrule tube fittings are chosen based on size compatibility for maximum sealing.
2. Chemical and Process Industries
Corrosion-resistant materials paired with accurate sizing ensure durability and safety in handling aggressive chemicals. Proper sizing minimizes dead volume and contamination risks.
3. Electrical and Instrumentation
Precision in tubing fitting sizes is vital for sensitive instrumentation, where small deviations can impair performance or cause instrumentation failure.
How to Choose the Correct Tube Fitting Size: Practical Tips
- Always measure the tubing accurately using calibrated tools.
- Match the fitting to the tubing’s OD and wall thickness.
- Consult manufacturer specifications and standards to verify compatibility.
- Test fittings under pressure before system commissioning to detect potential leaks or mismatches.
- Consider the application pressure and temperature as some fittings are rated for specific conditions, influencing size and material choice.
Advanced Considerations in Tube Fitting Sizes
1. Tolerance and Manufacturing Variability
Fittings and tubing manufacturing tolerate slight variations; thus, understanding tolerance levels ensures fitting integrity and system safety.
2. Connection Types and Compatibility
Different connection styles, such as compression, flare, and butt-weld, require specific sizing protocols, which must be adhered to meticulously to avoid mismatches.
3. Custom and Specialty Fittings
When standard sizes don't meet requirements, custom fittings are manufactured based on precise measurements, emphasizing the importance of accurate initial sizing data.
The Future of Tube Fitting Sizes in Industry
Technological advances continue to influence tubing fitting sizes. The integration of smart manufacturing, 3D printing, and AI-driven design enables more precise, durable, and complex fittings tailored to specific applications. As industries evolve towards automation and miniaturization, understanding size specifications and standards becomes more essential than ever.
Why Choose techtubes.in for Your Tube Fittings Needs?
Techtubes.in stands out as a trusted provider of high-quality tubing fittings, including ferrule fittings, forged pipe fittings, threaded pipe fittings, flanges, valves, and more. We prioritize precision in tubing fitting sizes to ensure compatibility, safety, and efficiency for your fluid systems. Our extensive inventory includes standard and custom solutions, backed by expert customer support and compliance with international standards.
Summary: Mastering Tube Fitting Sizes for Optimal System Performance
In conclusion, effective management of tubing fitting sizes is pivotal for constructing reliable, efficient, and safe fluid systems. From accurate measurements and understanding industry standards to selecting the appropriate connection types, every step influences the overall system performance. Staying informed and precise minimizes risks, reduces costs, and maximizes operational uptime.
For comprehensive solutions and expert guidance, trust techtubes.in, your premier partner in fluid connection technology. We are committed to providing top-tier tube fittings aligned with the highest standards of quality and precision.
Contact Us
Have questions about tubing fitting sizes or need personalized assistance? Reach out to our technical support team at [email protected] or call us at +91-XXXX-XXXXXX. We’re here to help you make the best choices for your fluid systems.