Custom Plastic Injection: The Key to Innovative Manufacturing
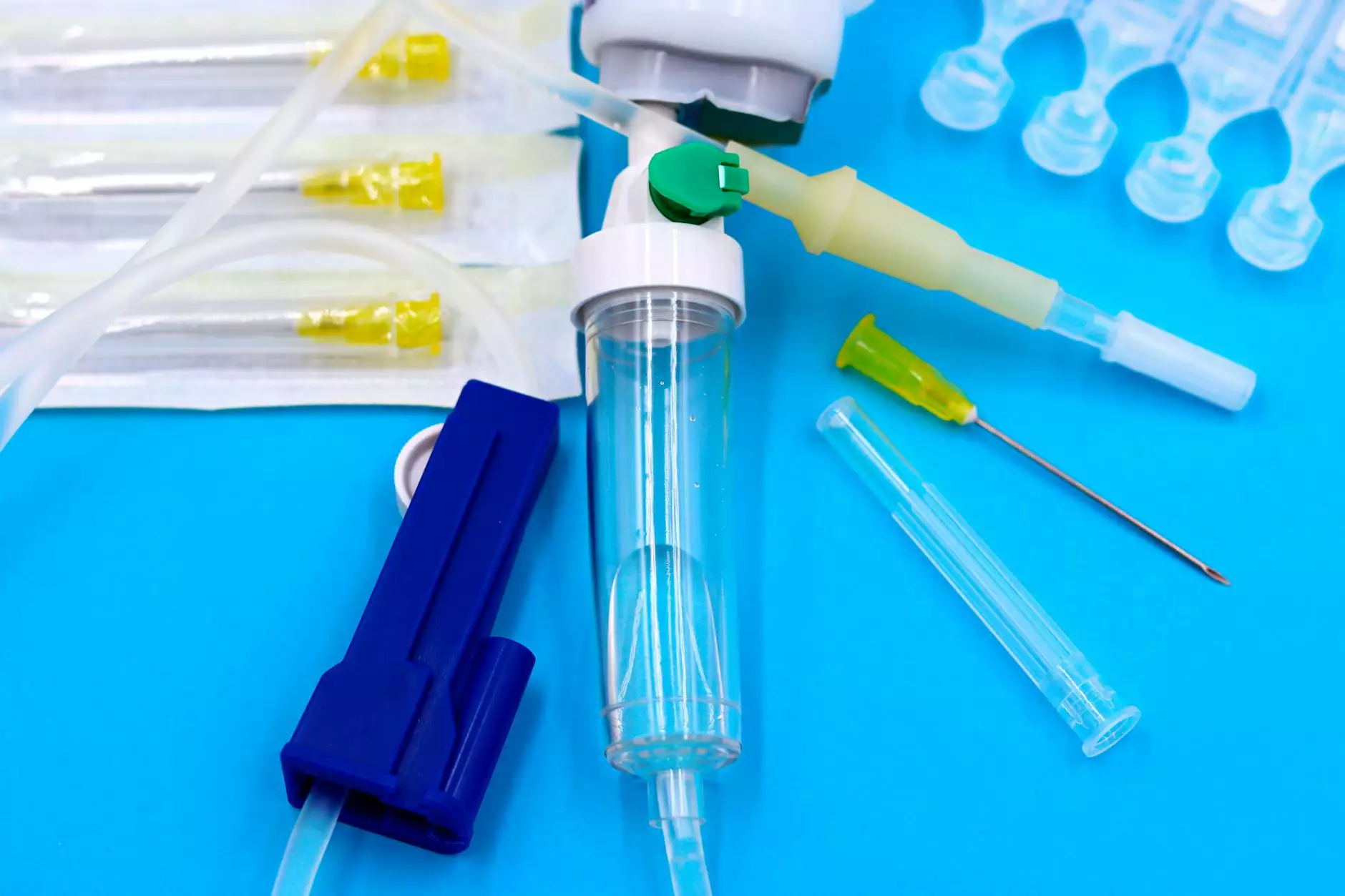
In today's fast-paced industrial landscape, the need for efficient, precise, and cost-effective manufacturing processes is more significant than ever. One method that stands out in the realm of production is custom plastic injection. This article delves deep into the world of custom plastic injection molding, exploring its advantages, applications, and the crucial role it plays in modern manufacturing.
Understanding Custom Plastic Injection Molding
Custom plastic injection molding is a highly complex process shaping heated plastic into specific forms using an injection mold. This technique is widely used across various industries to produce intricate parts with exceptional accuracy and finish.
How Does Custom Plastic Injection Work?
The process of custom plastic injection involves several key steps:
- Material Selection: Choosing the right plastic material is critical. Options can include thermoplastics, thermosetting plastics, and various specialty resins.
- Mold Design: Engineers create a precise mold to shape the plastic into the desired form, ensuring the design is tailored to the product’s specific requirements.
- Heating and Injection: The selected plastic material is heated until it becomes liquid and then injected into the mold cavity under high pressure.
- Cooling: After injection, the mold is cooled to solidify the plastic, allowing it to take on the shape of the mold.
- Demolding: Once cooled, the mold is opened, and the finished product is ejected.
Advantages of Custom Plastic Injection Molding
Custom plastic injection molding offers a plethora of benefits that make it a preferred choice for manufacturers:
- High Precision: Injection molding provides exceptionally accurate parts, which is essential for applications requiring tight tolerances.
- Efficiency: Once the mold is created, the production process is highly automated, allowing for rapid mass production of identical parts.
- Material Versatility: A wide variety of plastic materials can be used, enabling manufacturers to customize products based on specific needs.
- Cost-Effectiveness: Although the initial costs of mold creation can be high, the per-unit cost decreases significantly with large production runs.
- Complex Geometries: Injection molding allows the production of complex shapes and intricate designs that might be challenging to achieve with other methods.
Applications of Custom Plastic Injection Molding
The versatility of custom plastic injection molding makes it suitable for numerous applications across diverse industries:
1. Automotive Industry
In the automotive industry, custom plastic injection molding is used for manufacturing components such as dashboards, interior panels, and even functional parts like fuel tanks. The ability to create lightweight yet durable components helps improve overall vehicle efficiency.
2. Consumer Electronics
From smartphone cases to housings for appliances, the consumer electronics market relies heavily on custom plastic injection. This method enables manufacturers to produce intricate and sleek designs while ensuring durability and functionality.
3. Healthcare
Custom plastic injection plays a critical role in the healthcare industry, where sterile and precise components are necessary. Medical devices, surgical instruments, and laboratory equipment often utilize injection molded parts to meet stringent regulatory standards for safety and reliability.
4. Packaging Industry
Many packaging solutions such as bottles, containers, and caps are made using custom plastic injection molding. This enables manufacturers to create lightweight, versatile, and durable packaging options that meet consumer needs while reducing waste.
5. Industrial Supplies
The industrial supply sector benefits immensely from custom plastic injection molding, providing components for machinery, fixtures, and tools used in various manufacturing processes. The ability to produce robust and custom-fitted parts enhances productivity and efficiency.
Choosing the Right Custom Plastic Injection Partner
Selecting the right partner for your custom plastic injection needs is crucial for achieving optimal results. Here are several factors to consider:
Experience and Expertise
Look for a provider with extensive experience in the industry. A partner with a proven track record will understand the nuances of different materials, processes, and compliance standards across various fields.
Quality Assurance
Quality should never be compromised. Investigate the manufacturer's quality assurance processes, certifications, and testing standards to ensure reliable production and performance of your parts.
Technology and Capabilities
Evaluate their technological advancements, including their injection molding machines and design capabilities. Advanced machinery can lead to higher precision and efficiency in production.
Customer Service
A proactive and responsive customer service team can be invaluable. Ensure the provider maintains clear communication, addresses concerns promptly, and offers support throughout the project.
Conclusion
In conclusion, custom plastic injection molding is an indispensable technology in modern manufacturing, offering unparalleled precision, efficiency, and flexibility. Its applications span various industries, including automotive, consumer electronics, healthcare, packaging, and more. By choosing the right partner for your injection molding needs, you can harness the full potential of this innovative process, improve product quality, and enhance your market competitiveness. For top-notch custom plastic injection services, consider exploring the offerings at Sumiparts.us, where they combine cutting-edge technology with expertise in machining, laser cutting, welding, and industrial supplies.
Embrace the advancements in custom plastic injection to elevate your manufacturing capabilities and experience the remarkable benefits this process has to offer.